The frame
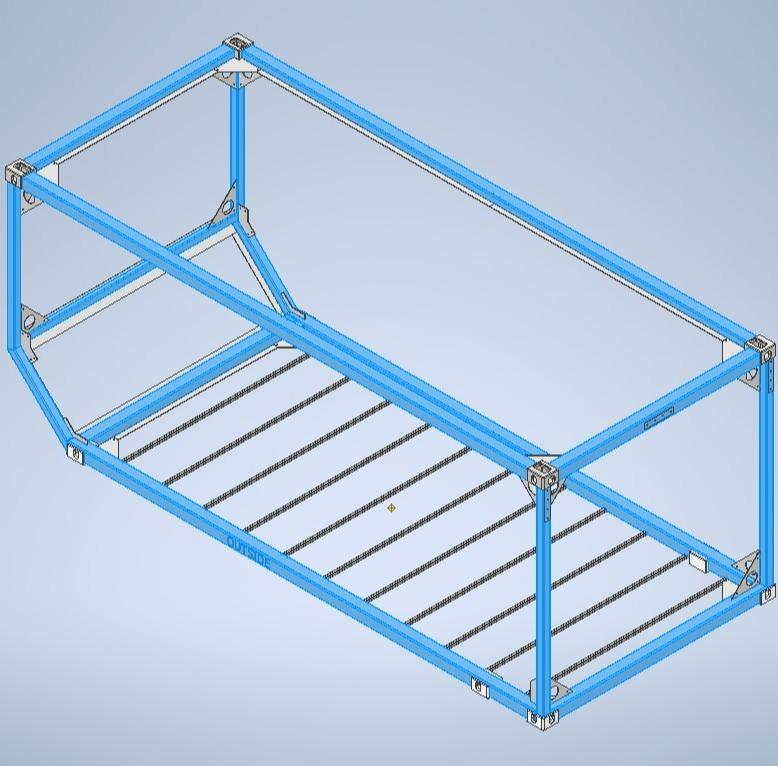
We can build the frame in any desired dimension and use corner castings to mount it with twist locks onto any truck. We believe that the box should be as independent as possible, as it is built to last a lifetime while the truck is changed or upgraded more frequently. This is particularly important considering the rapidly changing emission regulations.
The main beams for the frame are constructed using high-grade 120x120x6mm S355 steel, while the vertical beams utilize 80x80x5mm S355 steel. For frames longer than 6m or 20ft, the beams are upgraded to 160x160x6mm S355 steel. The floor consists of evenly spaced 30x30x3mm beams made of S235 steel, with an approximate spacing of 400mm. Additional beams can be added at specific locations such as for water tanks. Reinforcement triangles, made of 5mm thick S235 steel plate, are incorporated into the corners. If these triangles interfere with the door or hatch, we can make them slightly smaller.
A total of 8 vertical beams need to be installed along the length of the main beams to connect the lower and upper beams together, with 4 on each side. For instance, two can be positioned next to the door, and the remaining two can be placed near the end of the bed. These vertical beams can also serve as mounting points for various accessories or components. These vertical beams serve the purpose of connecting the lower and upper beams, thereby helping to distribute the weight evenly along the lower beam and upper beam. The entire frame is meticulously designed to fit together like a puzzle, with each component laser-cut to precise measurements. This level of precision ensures that everything can only be assembled in one correct way, eliminating the possibility of incorrect placement. As a result, the frame achieves a high degree of accuracy with minimal deviations.
After the welding process, the frame undergoes sandblasting to prepare the surface. Following sandblasting, it is subjected to a treatment method such as Feuerverzinken (hot-dip galvanizing) or Schooperen (spray galvanizing). This treatment helps protect the frame from corrosion and ensures its durability. Once the galvanizing process is complete, the frame is powder coated in any RAL color of your choice. Powder coating provides a durable and attractive finish, enhancing the frame's appearance and offering additional protection against environmental factors.
The panels
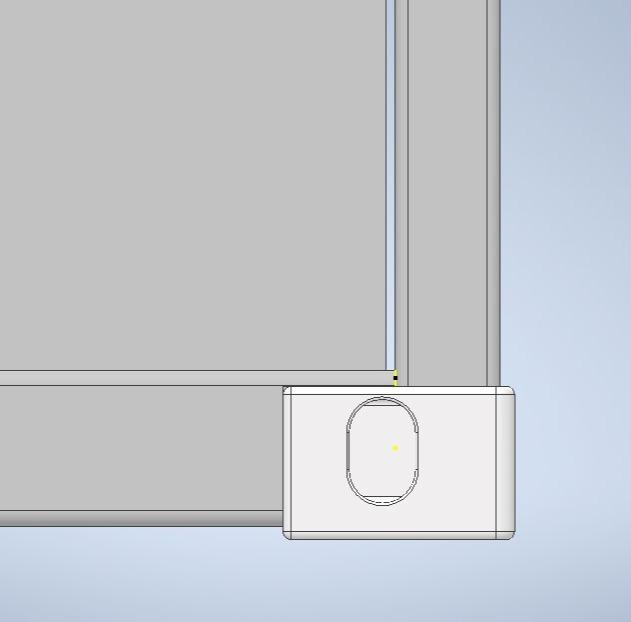
The panels we utilize are constructed with the following layers: Fiberglass 1.8mm - Honeycomb 5mm - PET70 Core - Fiberglass 1.8mm. The combined thickness of these panels is 60mm. It's important to note that this construction applies to all panels except for the floor panel. The floor panel, on the other hand, has an additional layer of PET150 measuring 15mm on top. Therefore, the floor panel has a total thickness of 85mm and is built as follows: Fiberglass 1.8mm - PET70 Core - PET150 15mm - Fiberglass 1.8mm.
The presence of the honeycomb layer in the panel design serves the purpose of dispersing direct heat from the sun away from the PET core. By creating a small air pocket between the honeycomb and the core, the heat transfer is minimized. This is particularly important when the panels are painted in darker colors. Without this design feature, the direct heat from the sun can cause delamination issues, where layers of the panel may separate or peel apart. The honeycomb layer acts as a thermal barrier, reducing the risk of delamination and helping to maintain the integrity of the panels, even when exposed to high temperatures.
The Fiberglass is Lamilux HG-4000 The PET core is ArmaPET Struct GR from Armacell
The panels are glued to the frame using a flexible adhesive from Henkel. This adhesive serves as an expansion buffer, accommodating the varying expansion coefficients of the steel frame and the panels. To allow for this flexibility, a 7.5mm gap is maintained between the frame and the panels at the top and sides. Furthermore, this gap is sealed to ensure proper insulation and protection. The sealing process helps prevent the ingress of water, dust, or other unwanted elements, maintaining the integrity of the structure.